Fake Organics
January 17, 2018
Fake news is all the rage these days, but personally, I’ve been waiting years for fake products to become more a focus of conversation. The fake products to which I refer are the ones that manufacturers and sales representatives market as “compostable” but in reality contain noncompostable plastic polymers.
In her 2016 blog article Death of Composting, Ayr Muir, founder and CEO of Clover Food Lab, a restaurant group in Boston, admonished composter Save that Stuff for no longer accepting compostable products. A longtime hauler of food scraps and compostable foodservice items, Save that Stuff had revised its policy to exclude compostable serviceware, to-go boxes, compostable cups, waxed or regular cardboard, and other paper products. In her blog, Muir wrote that her restaurants have been using all compostable products since 2010.
Other haulers adopted similar policies as several compost facilities in the Boston area announced they would only accept food scraps and would no longer accept compostable products. Institutions including the Massachusetts Institute of Technology (MIT), as well as businesses around the Boston area, were impacted.
Accepting just food scraps can make the composting process easier, as compostable products break down more slowly than food scraps. More importantly, however, post-consumer food scrap collection, especially when combined with paper and compostable foodservice items, is frequently more contaminated with non-biodegradable materials. Sometimes this occurs because “compostable” products are not fully compostable. It also occurs when food service workers, or customers busing their own plates, place plastics and other contaminants into post-consumer materials destined for a compost operation.
There are challenges to effectively diverting postconsumer food scraps and compostable products. But contamination can be successfully addressed through education. The experience of many compost operations has proven that working with haulers and customers can result in a clean stream of food scraps and certified compostable products.
However, there is no excuse for selling fake compostable products. And there’s a lot of harm done when those fake products are diverted to the organics stream. Compost operators are unknowingly processing items which do not fully degrade, which leads directly to the situation that restaurant owner Muir decried: many operations now refuse to accept compostable products because of the threat of contamination.
Meanwhile, consumers are told that these misleading products are compostable.
In 2002, standards for compostable products were established. These standards—ASTM D6400 and ASTM D6868 –establish specifications and tests that scientifically prove a material will biodegrade within a specific time frame, while leaving no persistent synthetic residues.
To guarantee that designated products are truly compostable, the Biodegradable Products Institute (BPI) adopted a certification program. Member companies whose finished products are certified as meeting ASTM D6400 and/or ASTM D6868 can use the Compostable Logo to provide assurance of compostability or biodegradability.
The program ensures credibility and recognition for products that meet the ASTM D6400 and/or D6868 standards, so consumers, composters and regulators know that products will biodegrade as expected. The logo is designed to be placed on the actual product as well on as packaging materials and sales literature.
Despite these and other regulatory efforts, a confusing array of so-called “compostable” bags and other products, complete with “greenwashing” labels – degradable, decomposable, biodegradable, etc.—continue to be marketed. Some products employ such misleading terms as “eco” or “bio.” The use of the color green for bags is yet another tactic used to market fake products.
Thankfully, two states and at least one municipality have taken on a leadership role in addressing the issue. In 2012, California mandated that products with the label “compostable” meet ASTM standards. Then, in 2013, the law extended the restriction to all plastic products, including containers, bags, straws, lids, and utensils; in fact, any consumer product and any kind of packaging claiming to be compostable have to meet ASTM standards.
Under California’s law, products labeled “compostable” or “marine degradable” must meet the applicable standard, specifically:
- ASTM D6400 for Compostable Plastics;
- ASTM D7081 for Non-Floating Biodegradable Plastics in the Marine Environment;
- ASTM D6868 for Biodegradable Plastics Used as Coatings on Paper and Other Compostable Substrates.
In 2017, Maryland adopted House Bill 1349, which requires products sold in the state and labeled as compostable to meet specific biodegradability standards. Starting in October 2018, plastic products labeled as compostable cannot be sold in the State unless they meet ASTM standards and the labeling guides in the Federal Trade Commission’s (FTC) Green Guides.
A 2011 Seattle ordinance bans single-use and biodegradable carryout bags. The ordinance was subsequently revised to address contamination from plastic bags in compost. The revised ordinance requires certain compostable bags to be labeled and tinted green. The purpose of the legislation was to reduce contamination of the City’s compost (food and yard waste) stream caused by customer misidentification and misunderstanding of which bags are compostable and which are not.
The legislation prohibits use of green or brown-tinted, non-compostable plastic bags for products such as vegetables, or for use as carryout bags. The ordinance also adds a definition of “compostable” to the code and requires that compostable bags be labeled as compostable.
Certified compostable products have a vital role in helping us to divert food scraps and compostable foodservice items from the waste stream. But until more is done to stop these fake compostable products, confusion and misunderstanding among institutions, commercial food scrap generators, haulers and composters are likely to continue. Without a more concerted effort to stop greenwashing, the organics industry will continue to face hurdles in capturing food scraps and organics from the waste stream.
By Athena Lee Bradley (with editorial input from Robert Kropp)
Share Post
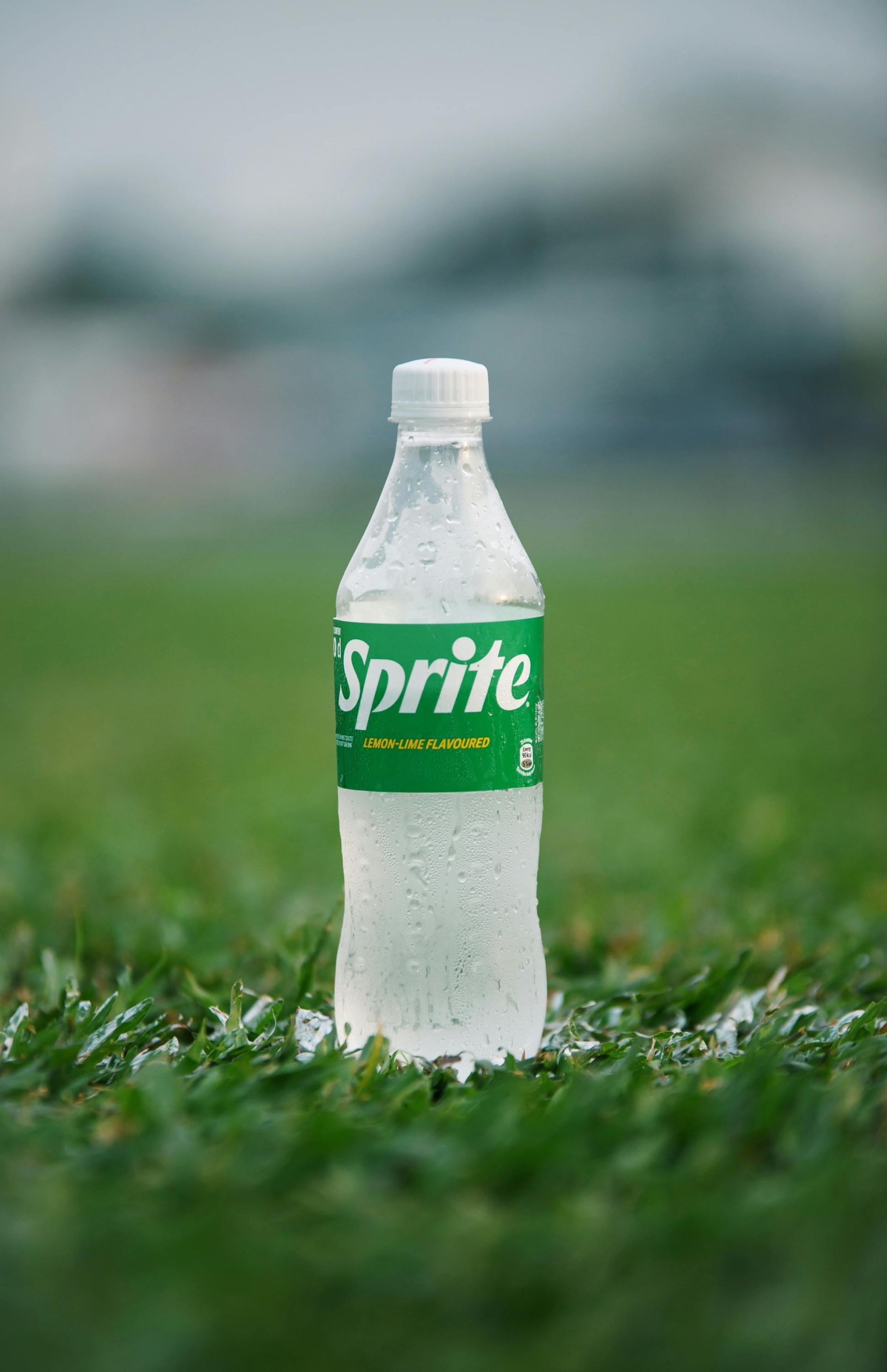
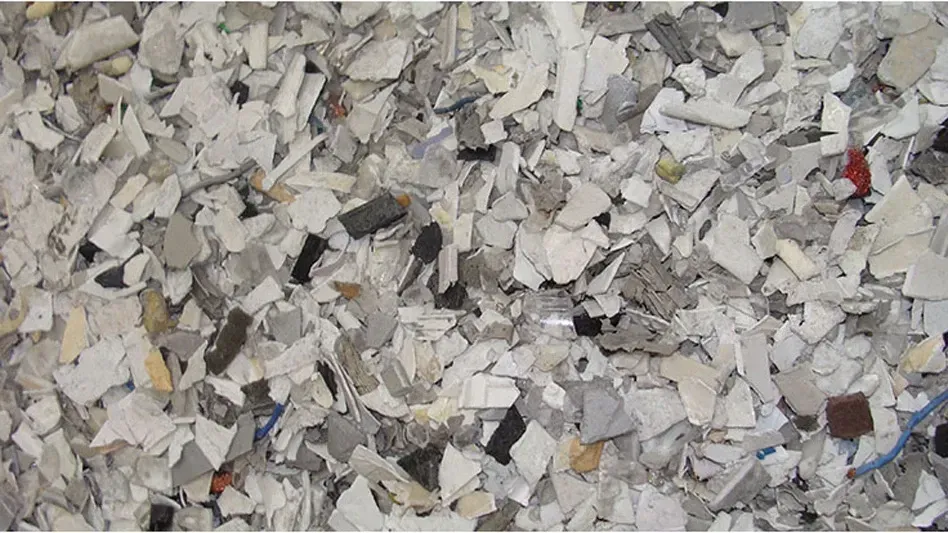
